Common Ice Machine Problems: How to Spot Issues Before They Escalate
Do ice machines often fail when you need them most? Many businesses struggle with unexpected malfunctions, leading to wasted time and resources. This article will outline common issues in ice machines, effective preventive measures, and tips for troubleshooting problems. Readers will learn how to identify warning signs early, ensuring their equipment runs smoothly. Addressing these concerns can help prevent costly repairs and maintain reliable ice production when it’s crucial.
Key Takeaways
- Regular maintenance checks are essential for preventing costly ice machine breakdowns
- Identifying signs of malfunction helps maintain service quality and customer satisfaction
- Proper water quality directly impacts the efficiency and lifespan of ice machines
- Engaging professional repair services ensures timely responses to ice production issues
- Establishing a maintenance schedule supports optimal ice machine performance and reliability
Understanding Common Issues in Ice Machines
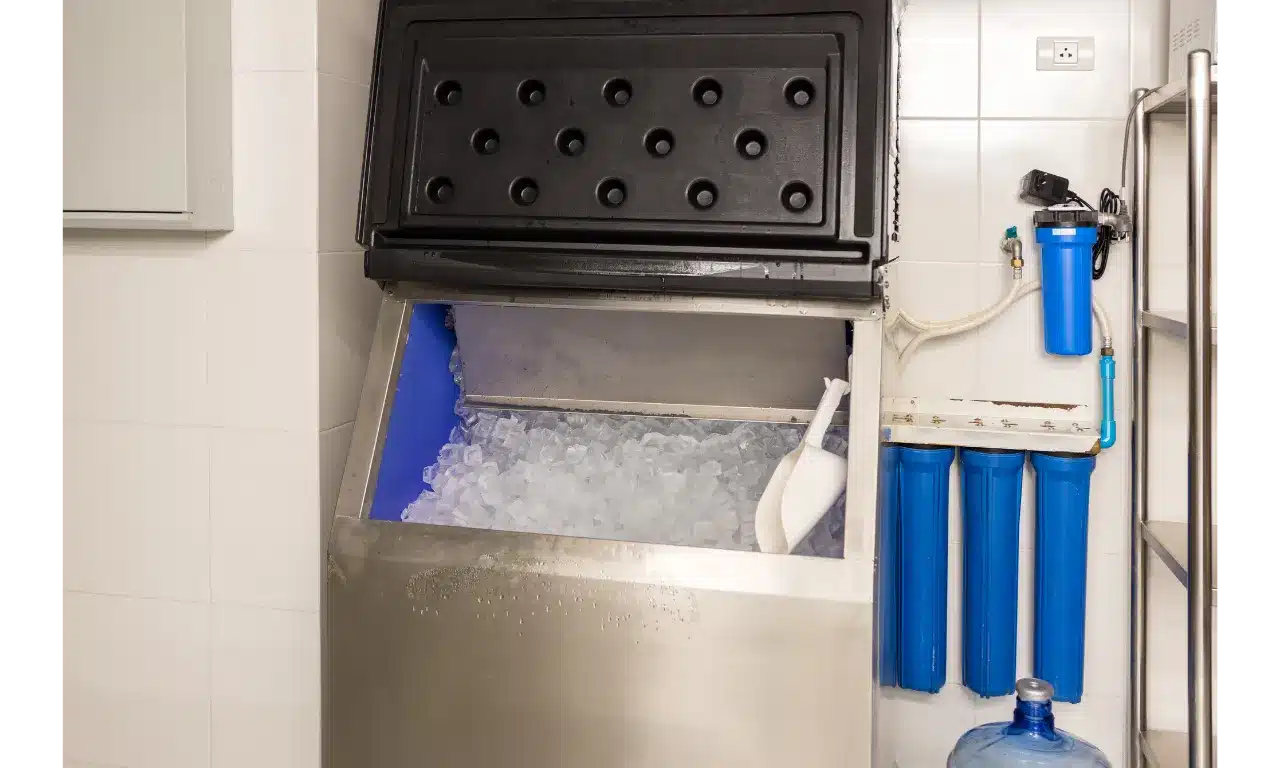
Recognizing signs of malfunction in ice machines is essential for ensuring consistent customer service. Factors contributing to equipment failures can vary, from improper installation to poor maintenance practices. Regular maintenance checks, including commercial ice machine services, are vital for extending equipment life, while identifying ice production problems can prevent costly downtime. Each of these aspects plays a significant role in maintaining optimal performance.
Recognizing Signs of Malfunction
Recognizing signs of malfunction in ice machines is vital for maintaining consistent ice production and service quality. Issues such as water quality problems, unusual vibrations, or delayed ice production can indicate underlying issues that require immediate attention. Regular inspection and professional ice machine services can not only identify these signs but also help prevent costly repairs and ensure the equipment operates efficiently, reducing the risk of interruptions that could affect customer satisfaction.
Factors Contributing to Ice Machine Failures
Various factors contribute to ice machine failures, impacting their efficiency and serviceability. Some equipment models are particularly susceptible to issues like clogged evaporators, which can hinder ice production. Engaging a reliable ice machine repair service for routine maintenance can prevent such problems from escalating, ensuring that the equipment remains in optimal working condition.
- Regular maintenance is crucial for identifying common issues.
- Clogged evaporators directly affect ice production rates.
- Utilizing professional repair services can enhance equipment longevity.
Regular Maintenance Checks and Their Importance
Regular maintenance checks for a commercial ice machine are crucial for identifying potential problems related to components like the thermostat and power supply. Knowledge gained from these inspections allows a handyman to diagnose issues early, preventing minor malfunctions from escalating into significant breakdowns. By addressing maintenance needs proactively, operators can ensure consistent performance and extend the lifespan of their ice-making equipment.
Identifying Ice Production Problems
Identifying ice production problems in an icemaker is crucial for maintaining operational efficiency. Common signs of issues include irregular ice formation or no ice production at all, often linked to compressor malfunctions or blocked water lines. Engaging a qualified technician can quickly resolve these matters.
Issue | Possible Cause | Recommended Action |
---|---|---|
No ice production | Compressor failure or clogged water line | Contact a technician for repair |
Irregular ice formation | Faulty thermostat or low refrigerant | Schedule maintenance check |
Unusual noise during operation | Loose parts or worn-out compressor | Inspect and secure components |
Ice machines face many problems, but these can be managed. With the right preventive measures, reliability becomes more than a hope; it becomes a certainty.
Preventive Measures for Ice Machine Reliability
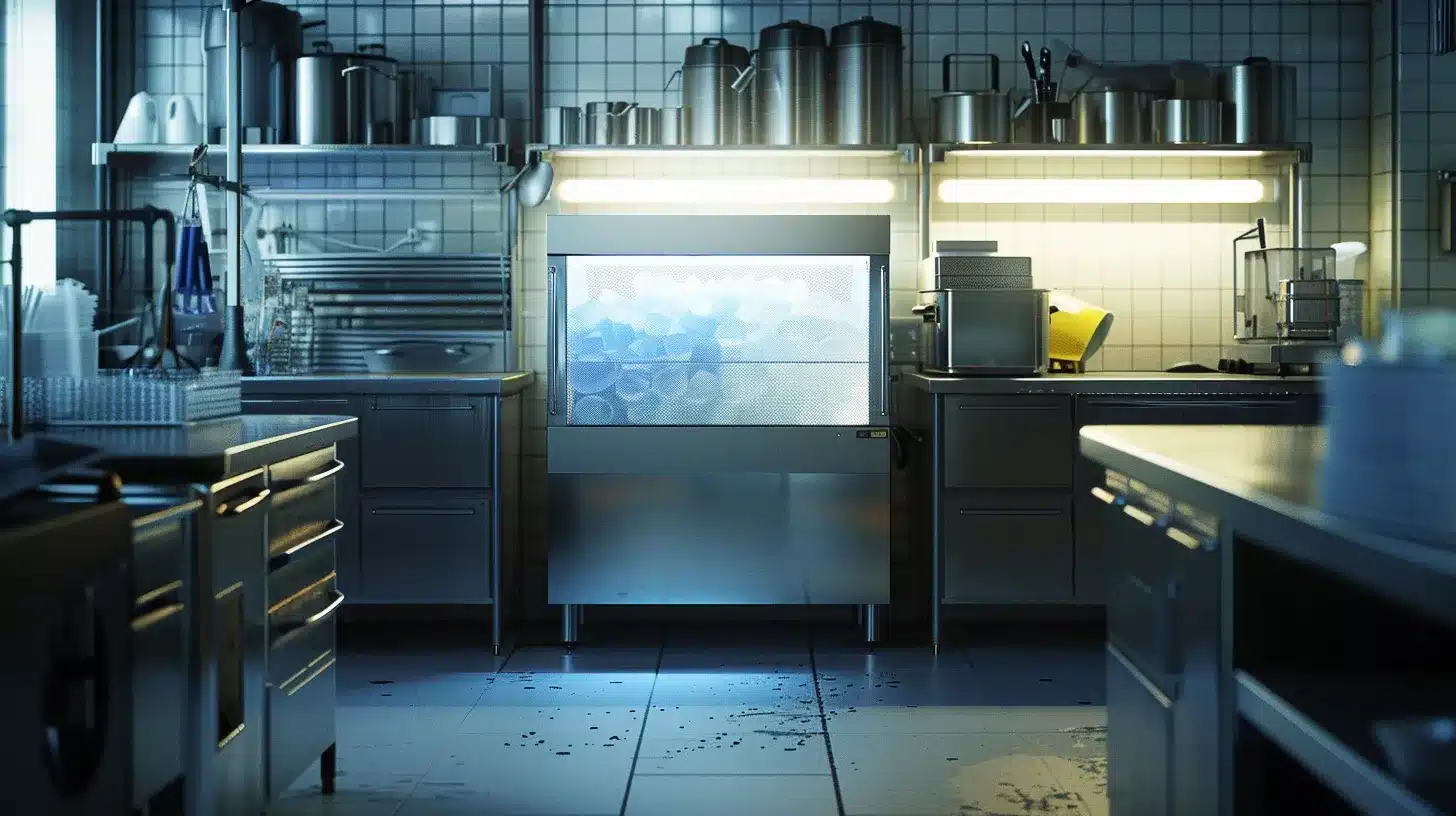
Establishing a maintenance schedule is essential for ice machine reliability, focusing on proper cleaning procedures and ensuring the water quality meets standards. Monitoring temperature and environment also plays a crucial role in preventing issues like leaks or malfunctioning parts, such as a heat exchanger. By proactively addressing these areas, operators can avoid costly appliance repair and keep their machines functioning optimally.
Establishing a Maintenance Schedule
Establishing a maintenance schedule for ice machines is a critical step in ensuring their reliability and efficiency. Regular troubleshooting practices help operators identify potential issues before they escalate into major problems, reducing the likelihood of costly repair expenses. This schedule should also incorporate proper filtration checks, as maintaining water quality plays a significant role in the overall performance and longevity.
Correct Cleaning Procedures for Ice Machines
Correct cleaning procedures for ice machines are essential to maintain their reliability and performance. Operators should routinely clean components such as the water reservoir and ice bin, ensuring that debris and mineral buildup do not hinder ice production. Scheduled maintenance performed by appliance repair services can offer expert guidance on proper cleaning methods and the importance of using the right cleaning solutions, which can extend equipment life and enhance overall functionality.
Cleaning Task | Frequency | Recommended Action |
---|---|---|
Clean water reservoir | Monthly | Remove debris and mineral deposits |
Sanitize ice bin | Every 3 months | Use approved cleaning agents |
Inspect and clean air filters | Monthly | Replace if necessary |
Ensuring Proper Water Quality and Supply
Ensuring proper water quality and supply is essential for maintaining the overall functionality of ice machines. Regular tests for contaminants and minerals can help identify issues that may lead to wear and inefficiencies. Operators should also monitor the circuit breaker status frequently to prevent unexpected downtime, as fluctuations in power can compromise the ice production process and potentially void warranty agreements if neglect leads to significant damage.
Monitoring Temperature and Environment
Monitoring temperature and environment is a crucial aspect of maintaining ice machine reliability. Variations in ambient temperature can affect the efficiency of the equipment, leading to potential issues in ice production. For example, a ice machine may struggle if it operates in an environment that lacks adequate airflow or has excessive humidity, impacting the water supply and energy consumption. Regular inspections by an appliance repair service can help ensure that the wiring and components remain optimized, preventing breakdowns and enhancing the overall performance of the machine.
Despite the best care, issues can still arise. Understanding how to troubleshoot these common problems will keep the ice flowing when it matters most.
Troubleshooting Common Ice Machine Issues
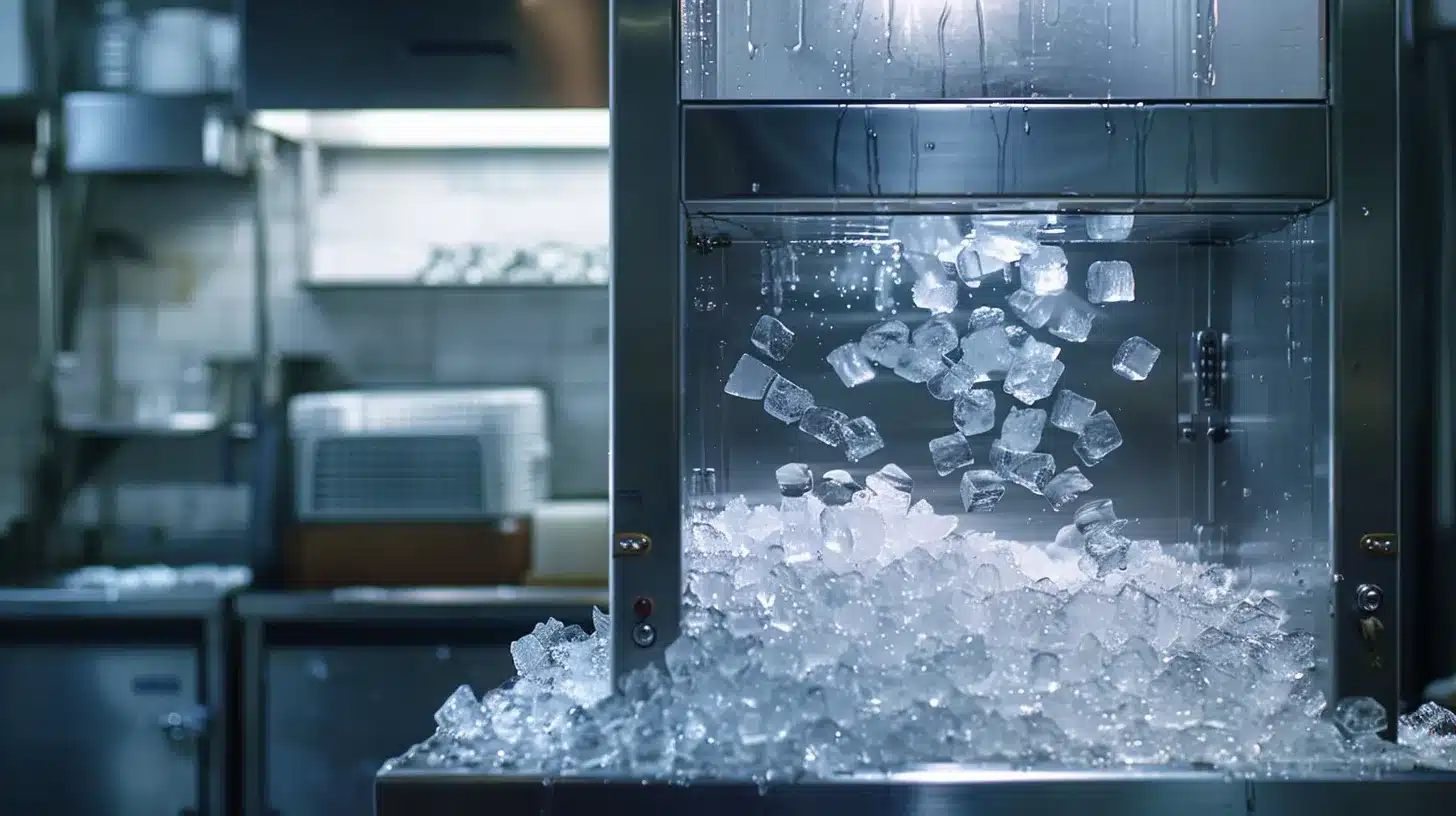
Addressing common issues with commercial ice machines is essential for maintaining efficiency and service quality. This section will cover strategies for tackling insufficient ice production, fixing blockages and clumps, resolving leaks and drainage problems, and correcting electrical and mechanical failures. By understanding these key areas, operators can prevent costly disruptions and ensure their equipment remains in peak condition while also addressing potential dust and debris buildup.
Addressing Insufficient Ice Production
Insufficient ice production in commercial ice machines can often stem from mineral buildup or a malfunctioning compressor. Operators should regularly check for internal clogs that may obstruct water flow and impede ice formation. By promptly addressing these issues, such as scheduling with a professional repair service or implementing proper leak detection methods, businesses can maintain consistent ice supply and reduce the likelihood of disruptions affecting service quality.
Fixing Ice Blockages and Clumps
Fixing ice blockages and clumps in commercial ice machines is essential for maintaining a steady ice supply and ensuring smooth operations. When ice builds up, it can lead to reduced production and potential malfunctions. To resolve these issues, operators should check the water lines for clogs and ensure proper airflow around the unit, as these factors significantly influence ice formation. Prompt action can prevent costly repairs and service fees that might arise from neglecting these common problems.
Resolving Leaks and Water Drainage Problems
Resolving leaks and water drainage problems in ice machines is crucial for maintaining optimal performance and preventing extensive damage. Common causes of leaks include faulty valves and improperly installed hoses, which can create noise and disrupt operations. Engaging reliable appliance service providers in Columbus can quickly address these issues, ensuring that your equipment stays in working order and minimizing the risk of water damage or inefficient ice production.
Correcting Electrical and Mechanical Failures
Correcting electrical and mechanical failures in ice machines is essential to maintain their proper function and prevent disruptions to service. Issues such as faulty sensors or poor airflow can lead to malfunctioning systems that affect ice production, ultimately leading to lower customer satisfaction. Operators should routinely inspect the ice maker for signs of electrical problems and consider scheduling professional ice maker repair services to address underlying issues promptly, ensuring the equipment operates smoothly and efficiently.
- Inspect for faulty sensors that may disrupt functionality.
- Check airflow around the unit to prevent overheating.
- Schedule regular ice maker repair to address mechanical failures.
- Prioritize addressing electrical issues to support consistent ice production.
Understanding common ice machine problems prepares one for the next step. Simple repairs can often bring these machines back to life and keep them running smoothly.
Typical Repairs Needed for Ice Machines
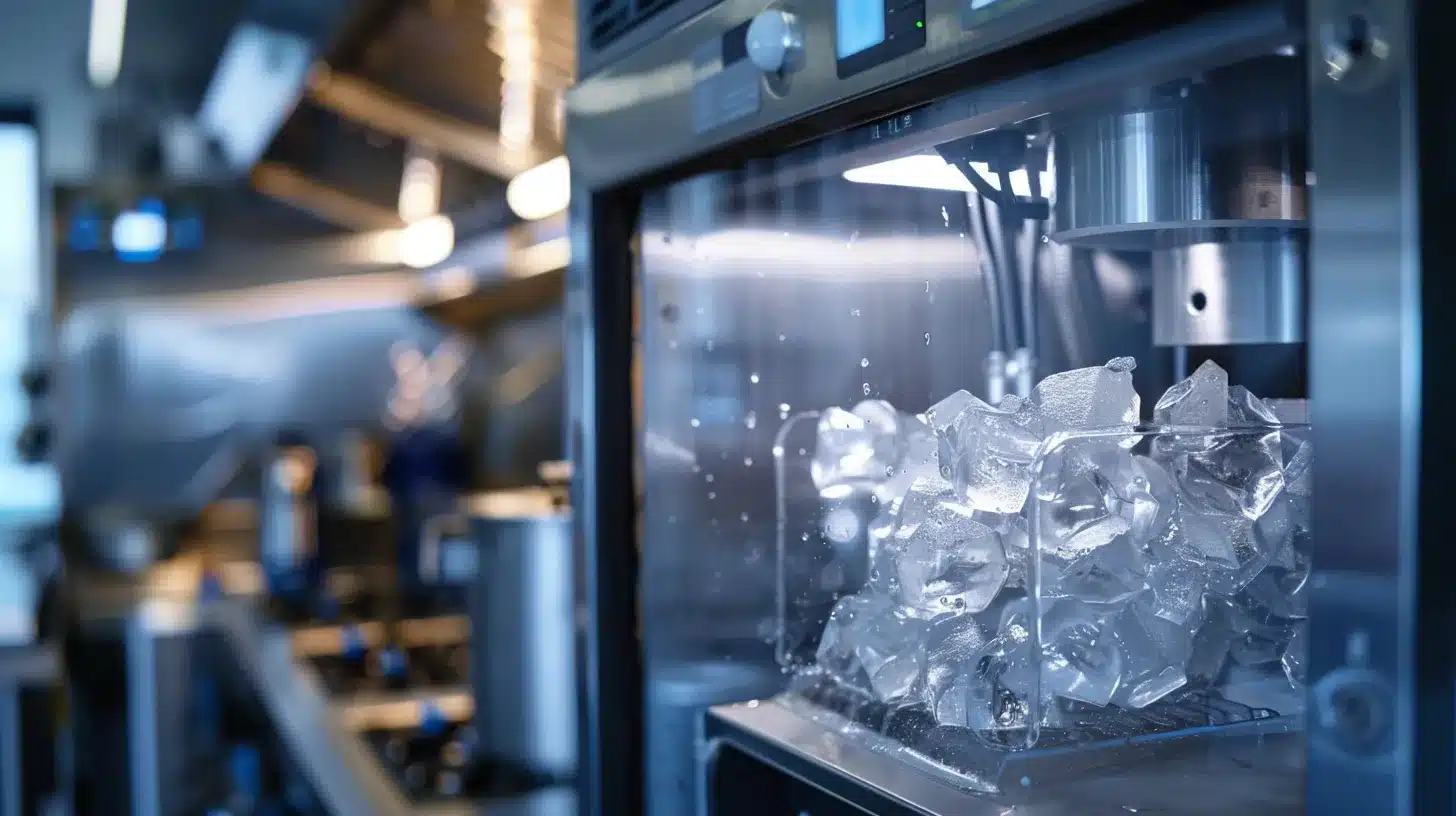
Identifying component wear and tear is essential for effective ice machine maintenance. During a repair visit, technicians evaluate issues like freezing problems and perform necessary fixes. Understanding the cost factors for repair and parts replacement helps operators budget for maintenance effectively. These insights ensure that ice machines remain functional, preventing interruptions in service and enhancing customer satisfaction.
Identifying Component Wear and Tear
Identifying component wear and tear in ice machines is essential for maintaining ideal performance and preventing breakdowns. Regular inspections can reveal signs of deterioration, such as unusual noise or irregular ice production, which often indicate issues like worn-out motors or damaged fans. By addressing these wear indicators promptly, operators can save on costly repairs and ensure their ice machines remain dependable for customer needs.
What to Expect During a Repair Visit
During a repair visit for an ice machine, technicians typically begin by conducting a thorough inspection to identify potential issues. They assess components such as the compressor, water lines, and electrical systems to pinpoint any signs of malfunction or wear. Following the evaluation, the technician will discuss their findings with the operator, outlining necessary repairs and estimated costs to ensure transparency and assist in decision-making regarding maintenance needs.
Cost Factors for Repair and Parts Replacement
Understanding the cost factors for repair and parts replacement in ice machines is essential for effective maintenance planning. Factors such as the extent of damage, labor costs for technicians, and the price of replacement parts can vary significantly based on the specific issue at hand. For example, a simple cleaning or minor adjustment may incur lower costs compared to a complete compressor replacement, which could be a substantial financial hit for businesses. By recognizing these potential expenses, operators can better prepare for necessary repairs and make informed decisions about maintaining their ice machines:
Repair Type | Typical Cost Range | Notes |
---|---|---|
Compressor Replacement | $1,000 – $2,500 | Higher cost due to complexity and parts needed. |
Thermostat Repair | $150 – $300 | Generally less expensive; quick fixes needed. |
Water Line Replacement | $100 – $500 | Costs vary based on location and accessibility. |
Repairs can leave one feeling overwhelmed and uncertain. Finding a trusted repair service can make a world of difference in getting ice machines back to work, ensuring peace of mind.
Choosing a Reliable Commercial Ice Machine Repair Service
Evaluating service options in Columbus is crucial for selecting a dependable ice machine repair service. Important questions to ask before hiring include inquiries about technician qualifications and response times. Additionally, looking for warranties and guarantees on services can provide assurance of quality repairs, helping operators make informed decisions and maintain their ice machines effectively.
Evaluating Service Options in Columbus
When evaluating service options in Columbus for commercial ice machine repairs, operators should prioritize companies that have a strong reputation and offer prompt response times. Inquire about technician qualifications to ensure they possess the necessary experience and training to handle various ice machine issues. Additionally, checking for customer reviews or testimonials can provide insight into the quality of service, helping operators choose a provider that can effectively address their maintenance needs and reduce the risk of costly disruptions in ice production.
Important Questions to Ask Before Hiring
When selecting a reliable commercial ice machine repair service, operators should ask critical questions to ensure they make an informed choice. Inquire about the technician‘s qualifications and experience in handling specific brands or models, as this knowledge can significantly impact the quality of repairs. Additionally, checking if the service provides warranties on their work can offer peace of mind, ensuring that if issues arise after repairs, the operator will receive the necessary support without additional costs.
Looking for Warranties and Guarantees on Services
When selecting a commercial ice machine repair service, it is vital to inquire about warranties and guarantees associated with their work. A reputable provider typically offers assurances, reflecting their confidence in the quality of repairs performed. This not only provides peace of mind for operators but also signifies the repair service‘s commitment to addressing any recurring issues that may arise post-repair, thus ensuring long-term reliability for ice machines.
Now that the right repair service is found, questions linger about caring for ice machines. This next section addresses those common queries, offering clarity for the maintenance journey ahead.
Frequently Asked Questions About Ice Machine Maintenance
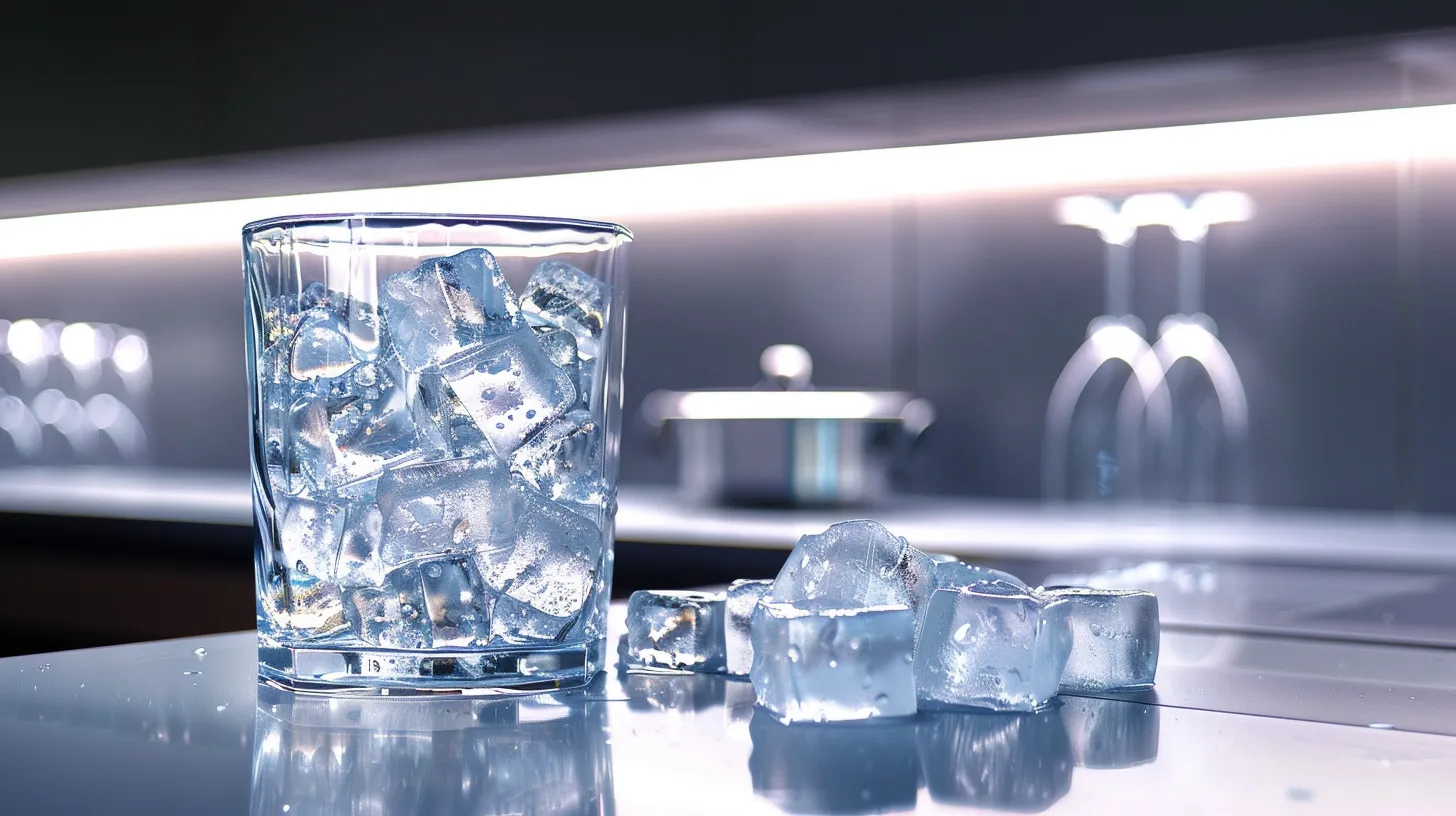
This section addresses key concerns regarding ice machine maintenance, including guidance on service frequency, factors influencing the lifespan of the equipment, and strategies for minimizing downtime. It also covers essential steps for effectively managing emergency repairs. These insights equip operators with practical knowledge to maintain their ice machines efficiently and prevent minor issues from escalating into major problems.
How Often Should Ice Machines Be Serviced?
Ice machines should typically undergo servicing every six months to maintain optimal performance. This regular maintenance schedule ensures that any potential issues are identified early, reducing the risk of costly repairs and downtime. Additionally, factors such as machine usage and water quality may require more frequent checks to address unique operational challenges and prevent ice production problems:
- Regular servicing supports consistent ice production.
- Monitoring water quality is vital for equipment longevity.
- Addressing issues early minimizes repair costs.
What Can Affect the Lifespan of an Ice Machine?
The lifespan of an ice machine can be influenced by several critical factors, including the frequency of maintenance, water quality, and environmental conditions. Regular servicing helps in identifying potential problems early, reducing the likelihood of significant breakdowns while ensuring optimal performance. Furthermore, poor water quality can lead to mineral buildup and other complications, ultimately shortening the machine‘s lifespan.
Factor | Impact on Lifespan | Recommended Action |
---|---|---|
Maintenance Frequency | Regular maintenance extends the machine’s life. | Service every six months. |
Water Quality | Poor quality can cause mineral buildup, leading to malfunctions. | Test and treat water regularly. |
Environmental Conditions | Temperature and humidity can affect performance and durability. | Ensure proper ventilation and climate control. |
Tips for Reducing Ice Machine Downtime
To minimize ice machine downtime, operators should implement a proactive maintenance schedule that includes routine checks for signs of wear and potential malfunctions. Regularly monitoring water quality can prevent mineral buildup, which is a common cause of inefficient ice production. Engaging with experienced technicians for timely service not only helps identify issues early but also ensures that the ice machine runs smoothly, thereby supporting consistent operations and customer satisfaction.
How to Handle Emergency Repairs
Handling emergency repairs for ice machines requires prompt action to minimize downtime and ensure continued operations. Operators should immediately identify the symptoms of malfunction, such as unusual noises or lack of ice production, and contact a professional technician to address the issue. Keeping a list of reliable repair services on hand can expedite the process and help maintain service quality during critical failures.
Issue | Recommended Action | Importance |
---|---|---|
Unusual noise | Contact a technician immediately | Prevent further damage |
No ice production | Schedule urgent maintenance | Ensure continued service |
Leaks | Shut off water supply and call a repair service | Avoid water damage |
Conclusion
Understanding common ice machine problems and recognizing their early signs is vital for maintaining consistent operations and customer satisfaction. Regular maintenance checks help identify issues such as clogged components or faulty sensors before they escalate into costly repairs. Operators must prioritize water quality and environmental monitoring to ensure optimal performance, reducing the likelihood of disruptions. By taking proactive measures and addressing potential problems swiftly, businesses can enhance the reliability of their ice machines and sustain service quality.